Essential Guide: The Importance of Installing Oil Water Separator
- ameliya lanne
- May 20
- 9 min read
Have you ever paused to think about what happens to oily wastewater after industrial processes? Maybe you’ve suspected there’s a high-tech method for dealing with it, but you weren’t entirely sure. If you’ve been curious about why businesses invest in oil water separator systems, you’re in the right place.
This blog post takes a friendly, no-nonsense look at how an oil water separator can transform the way industries handle oily runoff. We’ll explore the main components, compare different types, and answer pressing questions. By the time you finish, you’ll have a solid grasp of why this piece of equipment is widely considered a must-have for many Australian businesses.
Whether you’re trying to protect the environment, save money, or stay on the right side of local regulations, there’s plenty you can discover about separators. We’ll dig into practical benefits of oil separators, share real-life Aussie examples, and highlight common challenges. Ready to learn more? Let’s jump straight in.

Overview of Oil Water Separators
Oil water separators are systems specially designed to separate oil contaminants from water before the fluid is either recycled or released. These setups have become increasingly popular in Australia, where strict environmental regulations require responsible management of oily runoff. If you’ve ever wondered why many factories or businesses have a dedicated oil water separator in place, the answer often lies in the need to safeguard natural water sources.
Once the oily water enters the separator, the device draws on differences in density to remove contaminants effectively. Heavier water sinks to the bottom, while oil rises to the top for collection and disposal. This process may sound straightforward, but a well-constructed system can handle large volumes of wastewater daily, delivering a reliable safeguard for your drains, your site, and the broader ecosystem.
Why Installing an Oil Water Separator Is Essential
In many instances, untreated oily wastewater can wreak havoc on machinery, cause blockages, and even violate environmental laws. Businesses that refuse to manage their effluent responsibly might face fines and penalties. At the same time, they could see damage to their reputation if word spreads that they’re polluting local water supplies.
Installing an oil water separator ticks several boxes. First, it helps businesses meet legal expectations. Second, it protects rivers, lakes, and oceans from accidental pollution. Third, it reduces expensive repairs or system shutdowns by preventing oily build-up within sewage and drainage lines. All these advantages make oil water separators an invaluable investment, especially when long-term success and public image matter.
Oil Water Separator and How Does It Work
At its core, an oil water separator consists of a tank or chamber that allows oil-laden water to enter, settle, and then separate. You’ll typically spot internal plates or filters arranged to encourage oil droplets to clump together. By increasing the size of these droplets, the system makes it easier for them to float to the top. From there, a collection mechanism skims off the oil, leaving cleaner water behind.
Another important component is the coalescing media, which promotes oil droplet aggregation. This media might resemble rods or filters, and its main job is to boost the efficiency of separation. Some separators even have adjustable flow controls, which let you adapt performance to match specific conditions or volumes of incoming flow.
Oil Water Separator vs. Water Separator Compressor
While it’s easy to mix up these terms, an oil water separator differs from a water separator compressor. A water separator compressor is often part of an air compressor system, removing moisture from compressed air. In contrast, an oil water separator is built to extract oil from water so that wastewater can be discharged or reused more safely.
In some setups, you might have both devices operating side by side—one tackling moisture in compressed air, the other handling effluent from industrial processes. Understanding the differences is crucial if you’re shopping around for solutions because mixing them up could lead to an unnecessary purchase or a system that fails to meet your exact requirement.
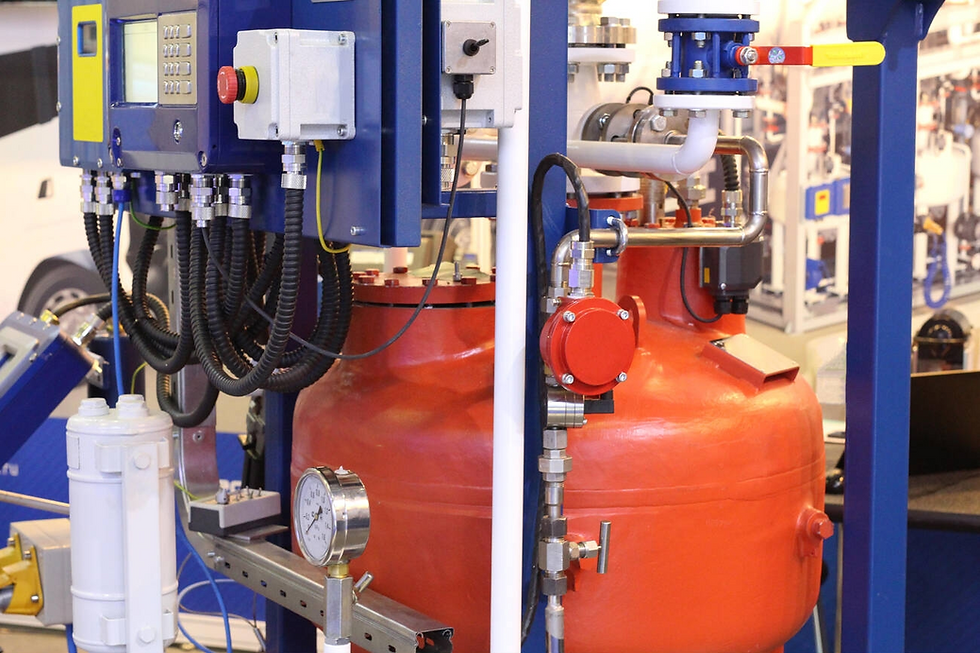
Types of Oil Water Separators
Air compressor water separators focus on removing condensate from compressed air systems. Over time, compressed air naturally produces moisture, which can accumulate and cause corrosion in piping and equipment. If that moisture contains traces of oil from the compressor, the entire system suffers. An air compressor water separator addresses this by separating water and oil before it recirculates.
For many commercial setups, these devices can be game-changers. By cutting down on moisture, they improve performance while reducing long-term wear and tear. While not the same as a dedicated oil water separator for wastewater, they still bring tangible value to industrial processes.
Benefits of Industrial Oil Separators
Financial Advantages and Cost Savings
One of the biggest wins for businesses installing an industrial oil separator is the potential for cost savings. If you regularly face fines or costly disposal fees for mismanaged wastewater, then implementing a system that automatically separates oil from water helps you sidestep those financial headaches. Moreover, avoiding blockages in your drainage infrastructure can spare you from expensive downtime or emergency fixes.
Beyond that, reusing treated water can offer even bigger savings. When you don’t have to keep buying fresh water for tasks like cleaning or cooling, you’re essentially reducing your overheads. Businesses that integrate oil water separator early often see a quicker return on investment simply by removing the expense of repeated repairs and penalties.
Environmental Impact and Compliance
Minimising environmental damage is the driving force behind many Australian regulations. Properly functioning oil water separators reduce pollution incidents, protect local wildlife, and help keep your standing in the community positive. Given strict regulations, especially for industries near waterways, compliance becomes simpler if your wastewater is already pre-treated before discharge.
Additionally, legislation often insists on thorough wastewater management protocols. By investing in an industrial oil separator, you’re demonstrating your commitment to sustainability. Plus, by meeting standards upfront, you avoid the stress and cost that non-compliance could bring.
Oil Separators Benefits for Equipment Longevity
Don’t underestimate how oily runoff can impact your machinery over time. When contaminants clog piping or build up in equipment, you face more frequent maintenance and potential breakdowns. The benefits of oil separators extend well beyond releasing cleaner water. They also safeguard essential tools, making them last longer and operate with fewer hiccups. Specific benefits of industrial oil separators might include more efficient cooling and reduced friction in mechanical systems.
The result? Lower operating costs and happier maintenance teams. By removing oil to an acceptable level, you’re keeping your entire production cycle cleaner. That can literally pay off when you look at your year-end accounts and see fewer pricey repairs.
Selecting the Right Oil Water Separator
Every industry has its own challenges. For instance, an automotive workshop might have small but continuous oil leaks from vehicle maintenance. A large manufacturing plant may produce thousands of litres of oily water each day. Begin by estimating your daily or weekly wastewater volume. Then, factor in whether the oil your setup produces is heavy, light, or even emulsified.
Understanding your specific configuration helps you pick the ideal capacity and design. Sometimes a simple gravity separator won’t cut it in a high-flow scenario. In that case, a coalescing system with a greater processing rate is usually the most sensible route.
Comparing Different Models and Capacities
Many suppliers offer a range of models, from compact units meant for small workshops to massive industrial installations. The brand name can hint at reliability, but don’t limit your research there. Look into specs like flow rate, expected oil removal efficiency, and required maintenance intervals. Some models promise “set and forget,” but you’ll still want to confirm how user-friendly they are in practise.
Make sure to gather quotes from different manufacturers or distributors. Ask about their track record with units installed in businesses like yours. That background information can be invaluable in choosing an option that aligns with your budget and meets your operational needs.
Checklist for Evaluating Suppliers
When comparing suppliers, consider their technical support. Does the company offer phone or on-site consultations for setup and troubleshooting? Another factor is spare parts availability. If a filter or seal fails, it’s reassuring to know replacement parts are easy to get.
As you gather details, keep a short checklist handy:
• Warranty terms and length.
• Customer reviews of reliability and after-sales service.
• Maximum flow capacity and performance data.
• Customisation options for unique industrial needs.
With these items in mind, you can confidently select a system and supplier that truly fits your circumstances.
Installation Best Practices
Before the separator arrives, map out the area where you’ll place it. Make sure there is convenient access for both installers and future maintenance checks. Look over any existing waste lines to see if they need cleaning or modifications to integrate with your new system.
Keep an eye on local regulations during planning. Some councils may require an inspection before you can even begin installation. Having all your paperwork ready will help you avoid potential holdups or fines down the track.
Maintenance and Troubleshooting
Regular check-ups are key to getting the best out of your oil water separator. Begin with quick visual inspections of the skimmer, internal plates, or coalescing media. Clear away any accumulated debris you spot. If your model includes a sludge or oil collection compartment, verify it isn’t nearing capacity.
A set maintenance routine helps you catch small issues early before they evolve into serious problems. This might include monthly filter changes or more frequent checks if your site handles a high volume of oily wastewater. Staying on top of all these little tasks ultimately saves you time and money.
Identify and Resolve Common Issues
If your separator’s performance seems off, check the flow rate. Too much incoming water can push oil through without sufficient time to separate. Another common culprit is clogged or damaged filters. Replacing them can often fix efficiency dips.
Sludge build-up is also a frequent concern, which can reduce space for proper separation. In that case, a thorough cleaning, or possibly a partial system overhaul, might be in order. If you’re in doubt, it never hurts to consult the supplier or bring in a technician.
Long-Term Performance Tips
For a long-running system, consistent record-keeping is a lifesaver. Record maintenance activities, note issues, and document how you resolve them. This allows you to identify emerging patterns or pinpoint recurring trouble spots. Aim to keep spare parts on hand, especially if your site is remote or tends to generate a large volume of oily water.
Moreover, consider scheduling an annual professional inspection. Experts can pick up on subtle signs of wear and tear, advising on upgrades or modifications that ensure your separator remains compliant and efficient.
Real-World Applications and Australian Examples
Industrial Case Studies
In Australia, many heavy-duty factories, like those in mining or metal processing, produce thousands of litres of oil-laden water every day. One Queensland-based facility installed a coalescing separator that lowered their oil discharge rate significantly. Not only did they pass environmental audits with flying colours, but they also cut waste disposal costs by nearly 25%.
Meanwhile, a large manufacturing plant in Victoria invested in an air oil water separator for its pneumatic network. The result was smoother production lines and fewer moisture-related shutdowns. These real-life success stories underscore the benefits of industrial oil separators in safeguarding equipment and trimming expenses.
Commercial and Retail Implementation
You might assume oil water separators are strictly for large plants, but smaller commercial spaces can also benefit. For example, petrol stations often have car wash bays. Water from these bays can easily gather oil residues and cleaning chemicals. A compact separator ensures the car wash water is properly pre-treated, helping the business remain compliant with council requirements.
Retail premises with onsite vehicle fleets may similarly rely on a smaller-scale solution. In each scenario, protecting local drains and waterways remains a prime concern. Whether big or small, the principle remains the same: separate the oil, preserve the water, and stay in line with local regulations.
Success Stories with Oil Water Separators
Several Australian automotive servicing workshops report major improvements in compliance after installing an oil water separator. In one instance, a small garage repeatedly exceeded the allowed oil levels in its discharged wash-water. After fitting a gravity separator matched to their output levels, they not only resolved the issue but also saw a positive reaction from clients who valued their commitment to the environment.
There are also Sydney-based warehouses that integrated both an air compressor water separator and a dedicated industrial unit. They effectively tackled moisture in their compressed air system while simultaneously managing large volumes of wash-down water. These multi-faceted solutions speak to the adaptability of oil water separator systems in varied situations.
Conclusion
Summing up, installing an oil water separator brings powerful advantages to businesses of all sizes. Whether it’s minimising your environmental footprint, extending the life of pricey equipment, or simply playing by the rules, the benefits of oil separators are hard to deny. From straightforward gravity models to advanced coalescing units, there’s a machine suited to nearly any operational demand.
Meanwhile, Australia’s strict regulations highlight how vital it is to handle oily waste responsibly. By using air compressor water separators or industrial oil water separators, you’re not only keeping your bottom line healthy—it’s also a way to support a cleaner planet. Feeling overwhelmed by all the options? Start by listing your must-haves, then seek professional advice to tailor the right solution for your specific needs.
Ultimately, the right oil water separator is more than just another piece of machinery. It’s an investment in productivity, reputation, and sustainable growth. Whether you’re a workshop owner or a manager at a major facility, now is the perfect time to explore your next steps. With proper planning and upkeep, your oil water separator can deliver years of reliable performance.
Comentarios